Cellulose ether, specifically Hydroxypropyl Methylcellulose (HPMC), is a commonly used additive in masonry and plastering mortar. Its unique properties make it an essential ingredient in the construction industry. In this article, we will explore the role of cellulose ether in enhancing the performance and functionality of mortar.
The primary function of cellulose ether in masonry and plastering mortar is to improve workability. HPMC acts as a water-retaining agent, ensuring that the mortar maintains its consistency during application. Without cellulose ether, the mixture would dry out quickly, making it challenging for workers to spread and apply the mortar evenly. HPMC helps to extend the workable time of the mortar, allowing for better adherence and reducing the need for frequent remixing.
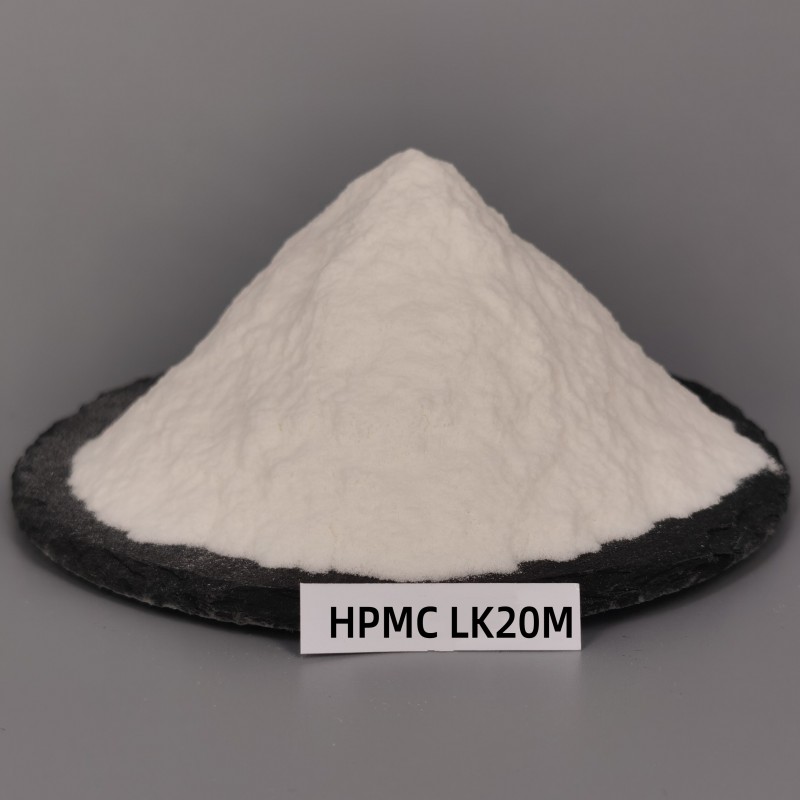
Another crucial role of cellulose ether in mortar is its ability to enhance the bond strength. When added to the mix, HPMC creates a thin film around the cement particles, which improves adhesion between the mortar and the substrate. This film also acts as a lubricant, reducing friction between particles, and preventing segregation during transportation and application. The improved bond strength provided by cellulose ether ensures a more durable and resilient finished product.
Cellulose ether also contributes to the overall water resistance of masonry and plastering mortar. The presence of HPMC helps to form a hydrophobic film on the surface of the mortar, preventing water penetration and subsequent damage. This water resistance is especially crucial in exterior applications where the mortar is exposed to harsh weather conditions. By reducing water absorption, cellulose ether helps to prevent cracks, efflorescence, and other moisture-related issues, resulting in a longer lifespan for the construction.
Cellulose ether plays a significant role in the control of shrinkage and cracking in mortar. The addition of HPMC helps to reduce the drying shrinkage of the mortar, which is a common cause of cracks. By reducing shrinkage, cellulose ether ensures that the finished product remains structurally sound. Moreover, the crack resistance provided by HPMC promotes better durability and aesthetics, avoiding the need for costly repairs or rework over time.
In conclusion, cellulose ether, particularly Hydroxypropyl Methylcellulose (HPMC), plays a vital role in masonry and plastering mortar. Its ability to improve workability, enhance bond strength, provide water resistance, and control shrinkage makes it an invaluable additive in the construction industry. With its numerous benefits, cellulose ether ensures that the mortar is easier to work with, more durable, and longer-lasting. Builders and contractors can rely on cellulose ether to deliver superior performance and achieve high-quality results in their masonry and plastering projects.
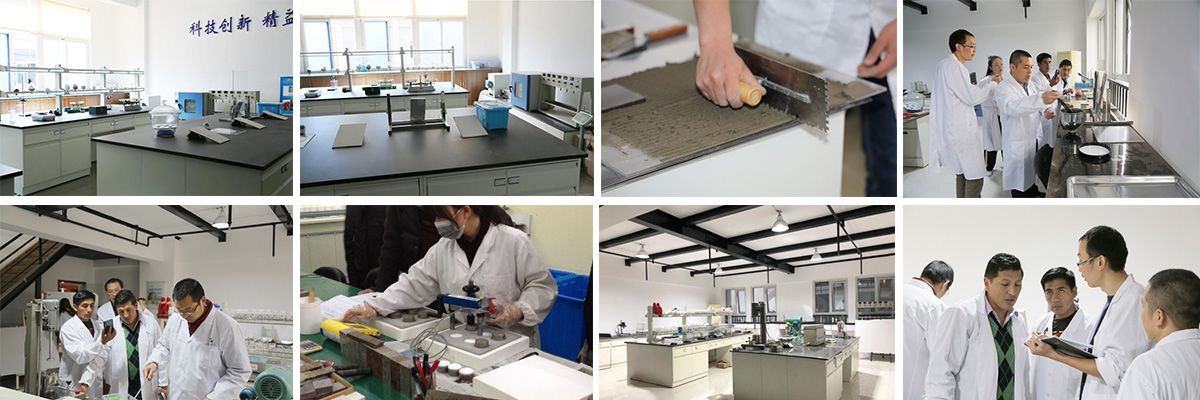
Post time: Oct-31-2023